
So, I’m at the point with the Flavonoid project that I need to start getting printed circuit boards made. (The printed circuit board includes an accelerometer, a real-time clock, touch sensor, and a bit of EEPROM memory, if you want to know.) A fair bit of the break was spent schooling up on Eagle, doing layouts, making mistakes and that sort of thing. (It’s remarkably full-featured for a free product and, despite a few quirks, does what it says it will do. Plenty of activity in the forums and help is quick to come when I’ve gotten in trouble.)As I closed in on a design I thought was close enough to gold to send off, I started poking around various forums to find out what operation might be suitable for small (1-10 piece) runs.
It turns out that most of the places you’ll hear about won’t do fewer than 5 pieces, and they’ll charge you for it, too. By way of example, I considered trying Advanced Circuits as the Spark Fun FAQ suggests them if you’re in a pinch for time. It’d have to be more than a side-project financed with my own wallet to use them, but maybe they’re better for big projects. (I compare them to the other two board houses near the end of this post.)
The one great exception is Batch PCB, the operation started up by the Spark Fun guys. They’ll do single pieces for, like..$2.50 per square inch. In my limited experience, that’s a great deal. In exchange, you’ll have to wait a bit longer to get your boards back — I think they’ve worked something out with their guy in China so that the numbers work out to get that kind of pricing.
The two places I’m trying are Batch PCB and PCB Fab Express. I picked PCB Fab Express because they had something they refer to as a special for prototypes, but it’s still pretty expensive (but less expensive than other places that’ll turn something around in under a week). I’m doing this so I know what my options are in the future. I can imagine times when waiting a couple of weeks is fine, and other times when I’d like to have something in a few days.
Batch PCB
This is Spark Fun‘s boardhouse operation, which I’d generally just use without even thinking twice, and I have, basically. The one small thing that makes it not necessarily a slam-dunk is the turn-around, which will be at least 10 days. But, that’s probably just fine, except sometimes I feel anxious. But, you know — it’s not like I have customers waiting for product or anything..just me. So, that aside, the Spark Fun guys are friends of the cause and so I support them whenever possible. What you’ll get are 2-layer (seems like they’re doing up to 4 now) boards with pretty much everything. No need to count vias or stuff. Silkscreen on both sides. 8 mil wires and a recommended 10 mils spacing. You can order one board if you want, which is fantastic (as opposed to most other places that make you order 5 of something for which you need only one, or which isn’t 100% yet, so you may end up getting 5 drinks coasters for your $100.) You can put more than one design in your board and just score the two, which can save you some trouble. They have one thing that most places don’t even think to provide — a simple, short-and-sweet Eagle tutorial on preparing your Gerbers. They have a hopped-up forum, where answers to your questions come back pretty lickity-split. Their DRC bot sends you a decent design review summary within a few minutes of uploading your Gerber .zip file (I’m still waiting to get back the DRC from PCB Fab Express, which I sent in a couple of hours ago.)
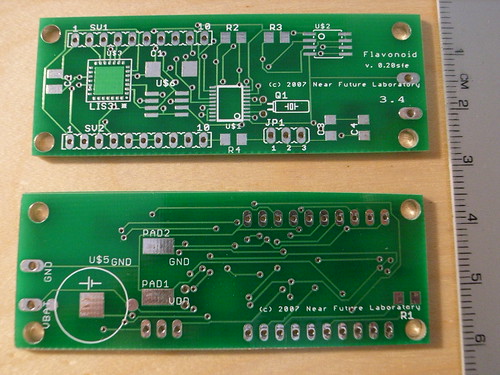
Flavonoid PCB’s just arrived from BatchPCB.com
All-in-all, this is the place to go if you can wait a couple of weeks for your parts. The PCBs you see above were sent in on December 28, and arrived on January 18. Considering generally delays during the holidays, and that Boulder (where those guys are) got socked in by a nasty blizzard, I’d say that’s satisfactory. Total cost for four boards with express shipping was $49.92 Compare to $82.95 for PCB Fab Express, five boards, five days, super-saver shipping. If you’re in a rush or just hopped-up and heads-down in a project, I’d guess the extra $30 is nominal. Note that PCB Fab Express won’t silk screen the back of the board, but that’s not such a big deal in most situations, particularly for prototyping.
One thing I noticed about the boards is that they’re not all 100% the same footprint. By this I mean that the way they were cut out of the larger panel (with probably lots of other people’s boards on it) resulted in slightly different dimensions. I mean, slightly. If you put the boards together like a sticks of gum in a pack, you can tell that some are slightly larger/smaller along the various dimensions. One even seemed slightly curved. This could be an issue if the packaging in which these boards are placed has critical sizing issues. But, it’s ever so slight — nothing that a fine file couldn’t smooth out, if it even caused a problem. (I’m talking about something that’s noticeable if you eyeball it, and measuring, it seems to be about 1mm or less discrepency in size.)
Summary: BatchPCB.com, four boards, silk screen on both sides, 14 business days turn-around, with a blizzard interfering, $49.92 with shipping.
Note that BatchPCB turn-arounds get shorter the more work they do as a company. Presumably, they are able to fill panels sooner and ship whatever minimums they need to their guy in China. Now (January 19) they say they’ll panelize a board in four days, so the turn-around is likely closer to 10 days or thereabouts. That’s fantastic. I also found BatchPCB to be much more “user-friendly”, as is generally the way with the Spark Fun team. (Their tutorials are excellent, particularly the one on does and don’ts for prototyping, all based on real experiences. Don’t forget their surface mount technology tutorials, too, found here. I had two situations where I needed to cancel an order I had submitted. Fortunately, it hadn’t gone too far into the cycle and they could delete the order. Their DRC bot is also quick and provides some useful graphics to give you a sanity check about what precisely you’re submitting.
PCB Fab Express
Okay, this operation seemed a little weird from the get-go, mostly because I got a call about 20 minutes after I created an account. (That sort of bothers me.) But, I talked to the sales guy and was assured that when I submitted by Gerber zip file, I’d get a design review check done and an email back. I submitted my Gerber zip file and must’ve misread something somewhere because my order was put “in process.” The board, my fault completely, had a ground plane copper pour that seemed okay, but I noticed that there were these friggin’ vias going through it. It was just all messed up, but I fixed it in about 3 minutes. Unfortunately, if they even had a DRC, it didn’t catch this (not sure it would’ve, even though it basically meant that nets that shouldn’t connect were connected.)
I tried to cancel it (calls and emails) but probably between a mix of my not being as attentive to what I clicked on and the holidays, there was no way to get the order out. I think there’s a problem in the Gerber I sent them, and I’m a bit surprised I didn’t get a DRC email or anything, but..well..I guess chalk that up to experience. (Update — it seems fine after eyeballing the boards I got.) Their prices are a bit more reasonable than other operations for the turn-around — 5 boards, 5 days, $82.95 with tax and “super saver” shipping. They’ll do a finer line spacing than is typical (6 mils). The largest drill hole they’ll do is 246 mils plated, which is fine, only sometimes a mounting hole might be larger, possibly. They have some restrictions on the average number of holes per square inch, which could be annoying if there are lots of vias or whatever. Two-layers, but no silkscreen on the bottom, which one can typically live with for a prototype.The boards just came in, which is exciting. The problem I thought I was going to have didn’t appear for some reason. Unfortunately, I over-wrote the board file from Eagle and so I can’t double-check what I sent them. (I could look at the Gerber’s, though.)
I don’t have all the parts yet, but just a cursory look-see and I thought of a few notes to think about for any redesign.

PCB Prototype Recto from PCB Fab Express 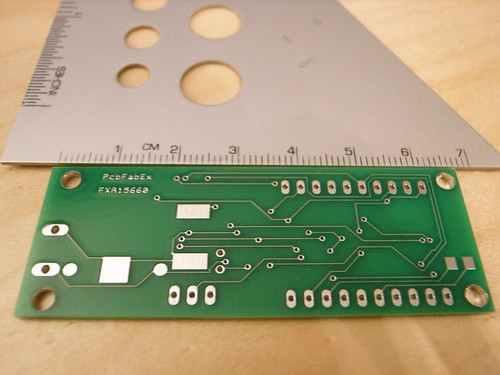
PCB Prototype Verso from PCB Fab Express. Notice there’s no silkscreen on the bottom.* First, some of the vias are unnervingly close to the pins of the DS1306. I’ll look for that in the future and put in a via keepout or something.
* Second, the crystal for the RTC I pulled from the crystal library. The pads for the package aren’t much bigger than a via, and there’s not much of a pad to speak of on the thru-hole. It might be just as well to find an SMT pad for it, or perhaps there’s a package in the crystal library for a surface-mount device.
* The mounting pin for the coin cell battery holder on the back is a bit close to the VBAT pad I put back there. I’m not sure if that mounting pin is connected to anything electrical in the coin cell holder, but I need to check just to be sure.
Summary: Quick turn-around. No hand-holding despite getting a sales call and promise of an email once I submitted. $82.59 with shipping for 5 boards, $16.52 per board, $6.19 per square inch. They took normal Gerber’s RS274X. I used the CAM processor user language program that Spark Fun provides for Eagle in their tutorial.
Advanced Circuits
Expensive and no real reasonable hobbyist pricing for a prototype option. This is probably “okay” for some situations, but certainly not for a hobbyist who’s just looking to get some boards done. No fault, no blame. Just thought I’d add it in since I went through the trouble of checking them out, but I won’t order from them.For comparision, I got a quote from Advanced Circuits for my test case — this Flavonoid PCB that you see above. For a “prototype” run, five boards in 3 days (the longest possible turn-around), it was $47 per board, or $235 without shipping. Their best value deal is 2 days, $57 per board. One day is $61 per board, and same day is $117 per board. Their production pricing — 50 units, say — is $5.86 per board in 2 weeks, or $7.57 a board in 3 days. So, roughly speaking, BatchPCB (described below) is priced in the same ballpark as Advanced Circuits’ production prices, even at single units. My BatchPCB boards came in 2 weeks and cost $7.50 a board ($2.50 per square inch, rounded up.)
Conclusion It’s hard for me to think why I would not use BatchPCB unless I really needed boards quicker than two weeks. If I need something in under a week, I’d go with PCB Fab Express. And, if I really am in some kind of project where I need dozens of printed circuit boards, I’d almost certainly go with BatchPCB — it’s just the best value.
If anyone has any suggestions of other board houses, please drop a line.
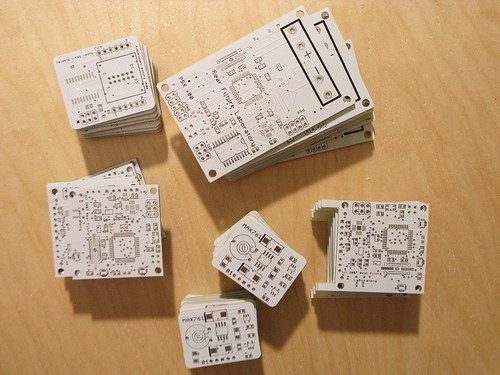
Update! I’ve been using Gold Phoenix when I need more boards as soon as possible — under a week. I haven’t completely run the numbers, but it’s pretty clear that for more than 10 boards or so, they’re the place to go to. If I need just singles of boards and can wait, I’ll use BatchPCB. I have a review of Gold Phoenix here.
For $89 (special summer deal pricing) you can get 1000 sq centimeters of PCB. When I put six designs on this size, I got 10 of each back. That’s 60 total boards. I paid extra to have some special features like white soldermask and black silkscreen and a $30 tax for multiple designs. Still, it seems like a great deal. Turn-around was under about 12 days.